– Vacuum forming – technology in which a sheet or film heated up to temperatures when the polymer turns into a highly elastic state is used as a blank. The pressure necessary to mold the parts is created by the pressure difference between the external atmospheric pressure and the vacuum created in the cavity between the sheet and the mold surface.
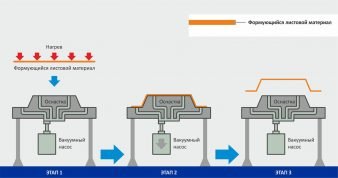
Vacuum forming process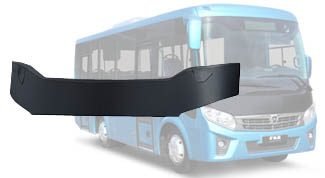
Variants of manufactured products
Application:
- Interior parts: Facing of instrument panels, door trim, tabletops;
- Exterior parts: Bus bottom frontend facing, trucks radiator grills.
Advantages:
- Thickness of the product can be from 01 to 10 mm, dimensions of the part can be 2-3 meters width and up to 1 meter height;
- Adjusted wall thickness of the part (due to different width of the plastic sheets);
- Possibility of production of small lots of parts or even single items;
- No seams at the part surface;
- Possibility of production of parts with required qualities of face surface (color, embossment/ graining, gloss, different kinds of impact resistance);
- Not very high level of investments in press forms;
- Project start up from 1 month.