– RIM (Reaction Injection Moulding) – technology of parts injection molding from unfilled polyurethane compositions. Liquid components based on high-molecular alcohol (polyol) and isocyanate are mixed in a mixing chamber and fed into the casting mold where the polycondensation reaction takes place.
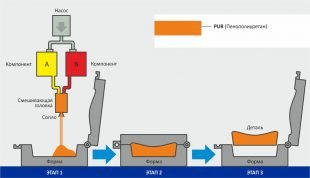
RIM process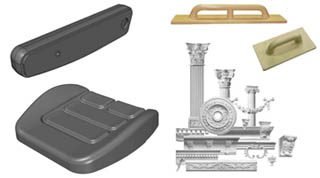
Variants of manufactured products
Application:
- interior and exterior parts: seat cushions, armrests, additional mirror body;
- consumer goods: construction graters, stucco molding, etc.;
- medicine: pillows, mattresses, seats, etc.
Advantages:
- Various wall thickness of the part;
- Wide opportunities of design;
- Embedded elements in part design;
- Short term of prototypes manufacturing;
- Not very high level of investments in press forms;
- Project start up from 1 months.
Various kinds of reinforcement fillers can be utilized at the technology. RIM is divided into the following technologies: SRIM, RRIM.
– SRIM (Structural Reaction Injection Moulding) – kind of RIM-technology in which reinforcing material (glass mesh, glass melt) or embedded parts are used to produce the unfilled polyurethane part with increased strength characteristics. The material is poured into the open mold.
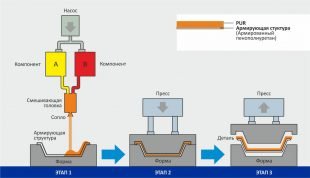
SRIM process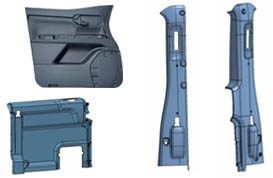
Variants of manufactured products
Application:
- Interior and exterior parts: part facing (doors, pillars, consoles frameworks);
- Medicine: pillows, mattresses, seats, etc.
Advantages:
- Premier-class surfaces due to combinations of simple technologies (IMС, Spray Skin, PMMA / АBS sheet);
- Light weight parts of high strength;
- Purposeful fiber orientation for wide opportunities of adjusting the strength parameters;
- Not very high level of investments in press forms;
- Project start up from 1 month.
– RRIM (Reinforced Reaction Injection Moulding) – a kind of RIM-technology, in which glass-powder / fiberglass is used as a filler to produce polyurethane parts with increased strength characteristics. Filling of the mold is carried out under pressure.
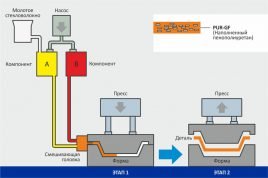
RRIM process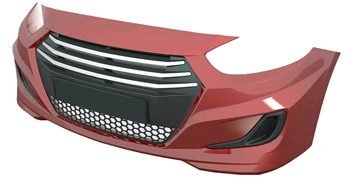
Variants of manufactured products
Application:
- Interior parts: door trim, instrument panel elements;
- Exterior parts: body parts, side moldings, front and rear spoilers, fenders;
Advantages:
- Close-toleranced dimension and maintaining its own rigidity even when exposed to temperature;
- Good colorability of the parts;
- Possibility of flow line painting;
- Short reaction time and production cycle – less than 90 seconds;
- Not very high level of investments in press forms;
- Project start up from 3 months.